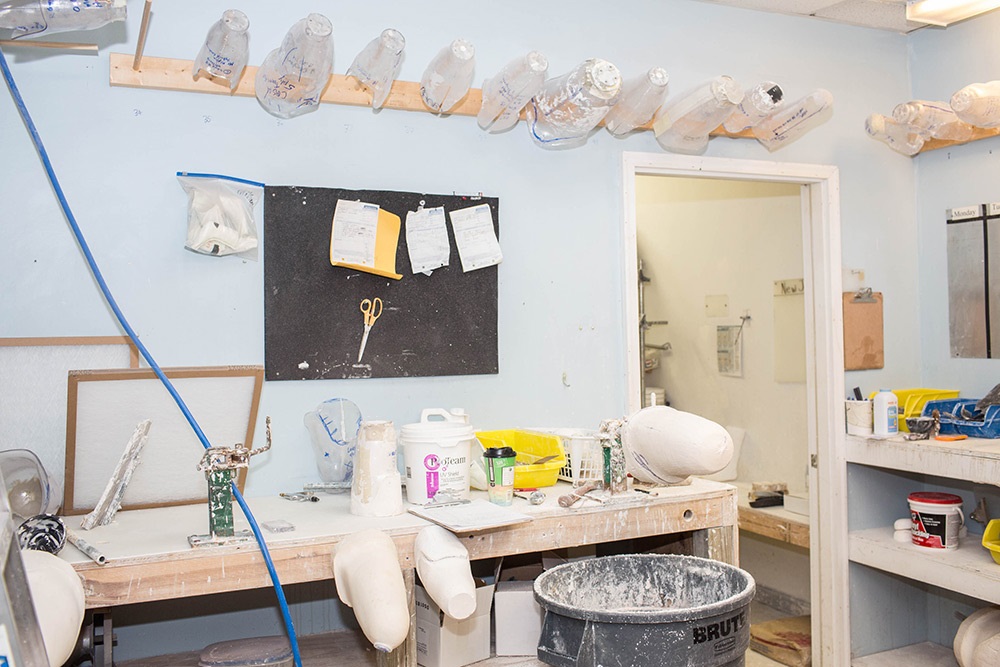
The Benefits of In-House Fabrication: Why Our 98% In-House Production Rate Matters to Patient
July 10, 2025
When it comes to prosthetics and orthotics, how and where your device is made can make all the difference. At Atlantic Prosthetic Services, we build nearly everything we fit—98% of our devices are crafted right here in-house. That’s not just a number we’re proud of; it’s a big reason our patients get faster service, better-fitting devices, and a more personal experience.
Let’s take a closer look at how keeping things close to home makes a difference.
Dramatically Reduced Wait Times
When prosthetic and orthotic components are outsourced to external fabrication facilities, patients often face extended waiting periods—sometimes weeks or even months—before receiving their devices or necessary adjustments. This delay can significantly impact quality of life, independence, and rehabilitation progress.
Our in-house lab changes everything. With complete control over the production process, we eliminate shipping delays, communication gaps with third-party vendors, and production queues at external facilities. The result? Our patients receive their custom devices and adjustments in days rather than weeks. In many cases, we can even provide same-day service, allowing patients to walk out with a functional prosthesis the very same day they're cast.
Precision-Focused Quality Control
Prosthetics and orthotics aren’t one-size-fits-all—they demand skill, attention to detail, and a deep understanding of each patient’s unique needs. By handling fabrication in-house, our clinicians stay closely involved at every step.
This hands-on approach allows us to inspect components throughout the process, make real-time adjustments, and ensure every device meets our rigorous standards before it ever reaches a patient. That level of care simply isn’t possible when outsourcing to third-party fabricators who don’t work directly with patients.
The result? Better craftsmanship, fewer fitting issues, and custom devices that align more precisely with each patient’s body and lifestyle.
Seamless Communication
In our in-house model, close collaboration creates a seamless flow of information that's critical for successful outcomes.
Our direct communication eliminates the misunderstandings and information gaps that commonly occur when working with external vendors, resulting in devices that better address each patient's unique circumstances.
Rapid Adjustments and Modifications
The initial fitting of a prosthetic or orthotic device is rarely the end of the process. As patients adapt to their devices, minor adjustments and modifications are often necessary to optimize comfort, function, and fit.
With our in-house lab, we can make these adjustments while patients wait, rather than sending devices off-site and asking patients to return days or weeks later. That kind of responsiveness can be a game-changer, especially early on during the critical adaptation period when patients are learning to use their new devices and when proper fit is essential for preventing complications.
For our patients with changing needs—whether due to residual limb volume fluctuations, activity level changes, or other factors—this responsiveness makes an enormous difference in their daily comfort and functional abilities.
Enhanced Innovation and Customization
With our fabrication capabilities in-house, we can more readily implement innovative techniques and technologies. Our team can experiment with cutting-edge materials, test new approaches, and develop customized solutions for unique patient challenges.
This flexibility is particularly important for patients with complex needs that don't fit standard protocols. Whether adapting devices for specific occupational requirements, athletic pursuits, or unique anatomical considerations, our in-house capabilities allow for truly personalized solutions.
The Human Element: Building Relationships and Trust
At the heart of everything we do is a simple belief: patients deserve to know—and trust—the people building their devices. Because we fabricate almost everything in-house, that connection is part of the process from day one. You’ll meet the same team that’s shaping your device, fine-tuning the fit, and making sure it works for your life—not just a standard template.
Our practitioners and technicians work side by side, combining clinical insight with hands-on craftsmanship. It’s not just efficient—it builds real relationships. We get to know your goals, your challenges, and what success looks like for you. That kind of collaboration helps us communicate better, adjust faster, and create outcomes that feel more personal and meaningful.
Experience the In-House Difference
At Atlantic Prosthetic Services, our 98% in-house production rate isn’t just a stat—it’s a reflection of how much we care about doing things right and doing them with you in mind. Whether you visit us in Wilmington, Whiteville, or Shallotte, you’ll get a team that’s close-knit, responsive, and deeply invested in your success.
You’re not just getting a device. You’re getting a team that listens, adapts, and stays with you every step of the way—so you can get back to doing what matters most.
READ MORE
Water Adventures with a Prosthesis: Your Beach, Lake, River, and Boat Guide
Plantar Fasciitis Relief: How Custom Foot Orthotics Can Help